
Submit feedback to Quanser about this page.\nonumber \]Īn example for determining these parameters for a typical process response curve to a step change is shown below. This example demonstrates the use of RCP CL Controller using PV gains.Ĭopyright © Quanser Inc. Of the error), which can lead to less overshoot in the closed-loop response.Īll input/output pairs of this function have direct feedthrough behaviour. Unlike the PID control, PIV feeds back only the measured velocity (i.e. Is used to compute the velocity of the error, where ω f is the cut off frequency. Instead, the first-order high-pass filter ω f s/(s+ω f) Minimize the noise in the control output. The PIV control loop is depicted below and has the following structure: Output, u is the controller output signal. Velocity gain, kv is multiplied by the measured velocity of the system and added to the final output.Įrror is the difference between the reference and measured signals, i.e. Integral gain, ki is multiplied by the integral of the error between the reference and measured signals and added to the final output. Proportional gain, kp is multiplied by the error between the reference and measured signals and added to the final output. desired position or velocity of a DC motor.
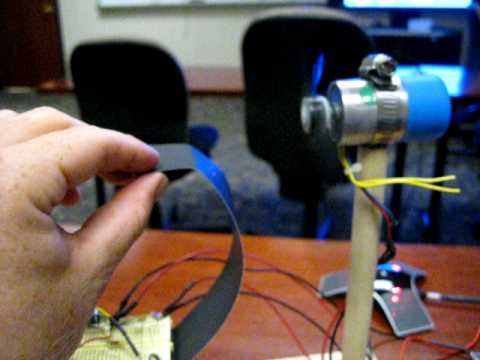
Reference, r is the reference signal, e.g. They appear in simple text in the context help window for the VI.Ĭut-off frequency is the high-pass filter cut-off frequency (in rad/s) used to determine the velocity of y. They may be selected to appear as terminals or dialog parameters, but show up as terminals by default. Produces a control signal that drives the system to the reference value based on the deviationīetween the measured value and the reference using Proportional-Integral-Velocity (PIV) control. Quanser Rapid Control Prototyping Toolkit, LabVIEW 2020 or newer,

Table of Contents > Quanser Rapid Control Prototyping Toolkit > VI and Function Reference > VIs - By Category > VI Categories > Continuous VIs and Functions > CL Controller >
